Build Up
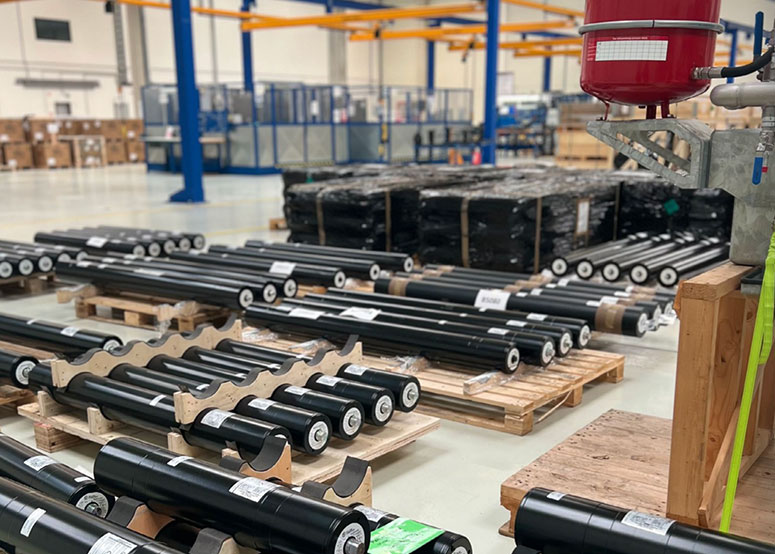
FEATURING: JOEL COX, GLOBAL SALES DIRECTOR, DELLNER WIND SOLUTIONS
AS SEEN IN: POWER AND ENERGY SOLUTIONS (PES) MAGAZINE
Being a manufacturer of components for wind turbines puts one in a perfect position to check the pulse, and temperature, of the industry. And, from this vantage point, it's evident that there are two patterns that are shaping the way we deliver our products and services.
The first trend we explore is the alarming transition to build-to-print from build-to- spec. Remember, wind energy was once a build-to-spec only sector; today, the direction of travel is very much to build-to- print, and it will have long-term implications in that the industry is cultivating a supplier base that can only produce at low cost, and we explain why.
The second trend, which we look at in an insert, is that the race to higher megawatt (MW) turbine capacities is slowing to the point where the industry has realised the wider benefits of consolidating rather than constantly upsizing.
Before all that, let's examine our credentials to commentate on these important subjects. The Dellner brand has been synonymous with industrial braking since Dellner Brakes was founded in 1941, but it has been a story of perpetual motion, right up to and beyond the 2021 acquisition of Dellner Hydratech, the Danish supplier of high-end hydraulic systems, cylinders, and accumulators for wind, offshore, and marine applications.
Other historic moments include the acquisition of Pintsch Bubenzer in 2018, leading to the formation of the Dellner Bubenzer Group.
At the centre of the range are heavy-duty rotor, yaw, and pitch brakes, used in various wind energy applications. Rotor brakes are typically caliper-style, active or passive, while rotor lock style pins, hydraulic or manual, are used for safety locking and maintenance purposes. Yaw brakes, active or passive, and sliding bearings, along with special brakes, are installed for pitch movement on the blades. Then there's high-end coolers, hydraulic systems, cylinders, and accumulators.
To help us tackle the two aforementioned subjects, we speak to a pair of stakeholders that spend their working lives immersed in this sector: Johnny Henrik Kjeldsen, Head of Research and Development Wind Solutions, Dellner Hydratech; and Joel Cox, Global Sales Director, Dellner Wind Solutions.
Component Builders
To understand the problems with this endemic, first we must establish what we mean by build-to-print and build-to-spec, sometimes called design-and-spec. Given that the second two are the same thing, we're only talking about two options in engineering and fabrication. Essentially, build-to-print and build-to-spec are different types of contract manufacturing.
Build-to-print is the process of building products to a client's work instructions. This method is often employed to make components or items of equipment that will be fitted in a larger machine. The customer will create a product drawing or design illustration that will include precise specifications; nothing is left to interpretation. Even the materials to be used are specified. The manufacturer's job is thusly to turn the drawing into a precise physical component.
With build-to-spec, the components are created by the manufacturer from scratch, based on their client's requirements. This is very different from build-to- print because the process allows for development and evolution of solutions to problems. The customer presents the issues they are having or the desired outcomes, and the manufacturer takes them away to design something based on what is combined decades of engineering knowhow and research and development.
Importantly, the manufacturer is involved from the beginning to the end, versus getting a drawing sent via email without ever having a prior discussion about the application at the point of use.
Cox says, 'I remember when OEMs (original equipment manufacturers) would connect with us at conception; they'd say they're building a new turbine, and these are the challenges they need a braking solution to overcome. Now, there's been a huge shift and no turbine manufacturers are bucking the trend.
'We're now working in a build-to-print not build-to-spec marketplace. That would have been a shocking revelation even as recently as a few years ago.
'Nowadays,' he continues, 'we're given a drawing, and the maths has already been done for us; we just passively build what's on the piece of paper. It's dumbed down our engineering; that changes things. OEMs have limited resources and are not equipped to drive component innovation.'
Kjeldsen adds, 'As the price pressure in the wind industry grew, the need for multiple suppliers on the same products grew with it. The price had to be challenged and the best way to do that was by having multiple suppliers. If each supplier had their own product, the work for a wind turbine manufacturer's R&D would be very high since it was a new design from each supplier with different documentation.
'This created the idea of introducing build-to- print: one product from all suppliers, and only one product to maintain and document. It is easy to compare price between suppliers, and easy for procurement to get pricing from new suppliers since a complete documentation package was already available. By not using the expertise and knowhow in specialised manufacturing fields, OEMs have to come up with the ideas and innovation themselves.'
It can be argued that the key advantage of build-to-print is a perception of accuracy and efficiency; when the customer has their drawings, they can repair items and build to specification quickly. It's a type of replication and repeat manufacturing process. However, it doesn't allow for investigation into why a part might have broken or failed and neglects to allow for continued improvement of manufacturing processes.
Kjeldsen comments, 'Where build-to-print works really well is when having a product where a lot of innovation and new design is not needed. The input from suppliers to improve the product is not required, so it has moved into a phase where it is more a commodity product. Low-cost is the driver not innovation.
'The main problem with build-to-print,' he continues, 'is that the suppliers are not able to utilise their R&D power to the full extent. The products are already fully designed and documented. It removes the incentive to compete on R&D skills and resources. The supplier is reduced to being a production hub.
'Competition is now primary low-cost production and goods procurement and logistics. There is no incentive to invest in R&D and technology. Consider the long-term implications that has on a sector like wind energy.'
In conclusion, while there is a place for both build-to-print and build-to-spec in manufacturing generally, the latter is clearly favourable when we are talking about the myriad of highly engineering components, say, on a wind turbine.
However, as Kjeldsen argues, 'The value of build-to-spec has in my opinion not returned to the industry. It is still moving in the direction of build-to-print. Today's customers are not interested in innovation, collaboration, and new ideas. Suppliers are competing on low-cost and not innovation of the products that they rely on to keep them safe and productive.'
Cox concludes, 'The industry has slowed its investment and component sectors, each of them universes of engineering brilliance in their own right, are competing on cost not pace and strength of innovation. Farcically, sometimes they're even prepared to pay more to fit a square peg into a round hole because it's what the build-to-print drawings say.
'We need to champion the benefits of build-to-spec and return to a model where our engineering expertise in heavy-duty rotor, yaw, and pitch brakes is given due opportunity to drive continued improvement of industry best practices.'
Bigger isn't always better
For a long time, wind energy original equipment manufacturers (OEMs) were constantly striving to make higher megawatt (MW) turbine capacities. Mingyang Smart Energy announced the MySE 22MW at the China Wind Power 2023 exhibition in Beijing.
Joel Cox, Global Sales Director, Dellner Wind Solutions, says, 'It was a trend that started onshore and then went offshore. I understood it in theory, but the industry didn't scale it correctly.
'It was also true that there were geographical nuances in play in that Europe generally has less space for multiple turbines, whereas in the US, in places like Ohio, there is a much greater landmass where multiple turbine farms can be built with little impact on public life or other infrastructure.
'Seemingly, one moment we were talking about five and six megawatt turbines; then 15, 16, 18, and upwards was on the table. Then we were hearing about 30 MW test machines and plans to build a 35 MW model. It was like a competition; we wondered, where would it end? One of my heroes is Nikola Tesla and he would have no doubt pleaded for common sense and said, 'Hold on, enough is enough'.'
Cox continues, 'This trend has abated, and the focus is, thankfully, now more on making the existing products profitable versus upscaling them. I'd rather have a long-term plan built around a tried, tested, 15 MW turbine than try to push the boundaries. If we need 30 MW of power, how about two 15 MW turbines? That's better.'
This has generally been a positive reset by the industry. Let's hope the same sense of reason can be applied to the issues around build-to-print and build- to-spec, as discussed in the main body of this article.
VIEW ARTICLESEE PAGES 48-51